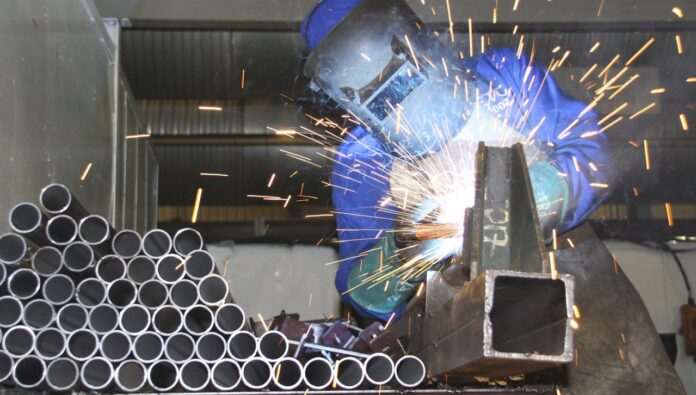
Metal is a vital material used in manufacturing, construction, and all kinds of other industries. Pretty much everything we use has metal in it somewhere, from the cars we drive to sewing needles and kitchen appliances. Without metal, modern life would look very different! This is a truth that has been known for a while now. Nothing changed in the past hundred years, and we don’t see it changing in the foreseeable future.
Metal fabrication is often associated with welding, but that’s not the whole story. Fabricating metal doesn’t just involve heating it up until it reaches a melting point – it involves a variety of different techniques. In this article, we are going to try and lead you to this process, so you could understand metal fabrication better.
Metal Fabrication Workshops
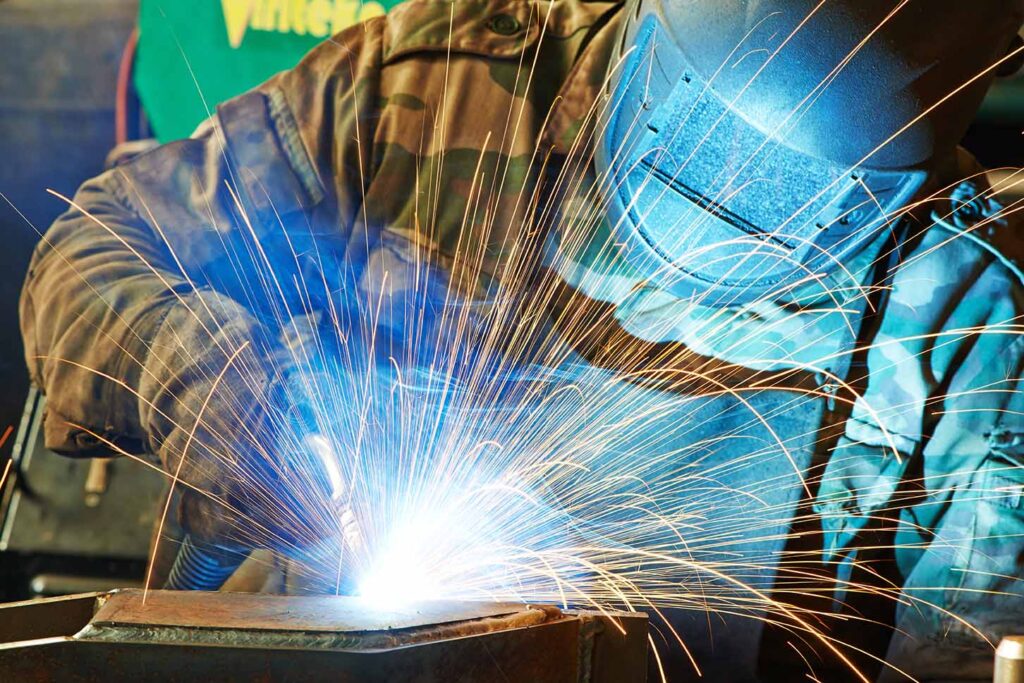
Metal fabrication companies like The Federal Group USA bend and shape metal into parts and end-products. These parts are used as standalone pieces, such as tools, or used to create a larger item, such as a car or truck. Metal fabricators begin with sheet metal. This is cut into smaller pieces and sent through a production line or worked on a smaller scale, depending on the scale of the operation. But before we reach that stage, we have to design the product we need.
The Design Process
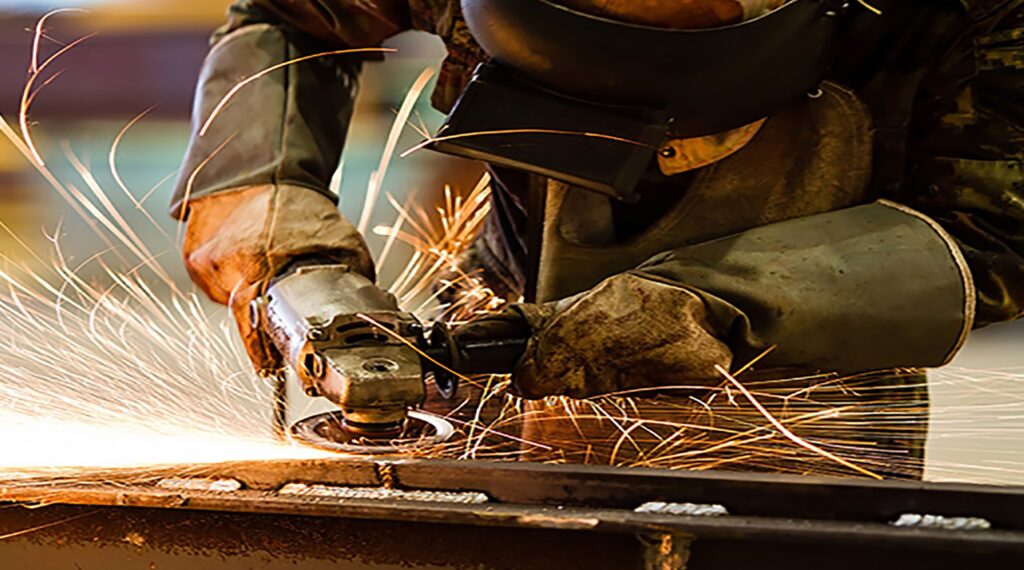
Metal fabricators can work with a design or a prototype. Designs are created using CAD and CAM software. The design is then used to create a prototype, so the designer can check for flaws in the design and decide whether or not the design is actually viable. After all, it is vital that the product actually works as intended!
There are many different metals, all of which have different properties and use cases. For example, steel is typically used for large engineering projects because it is strong and malleable, whereas a more expensive metal like zinc might be used for more precision fabrication designs.
Part of the design process is deciding which metal to use. This is why a prototype is so useful, as the designer might assume one metal has all the right properties but upon fabrication, it transpires another metal that is more suitable.
Fabrication
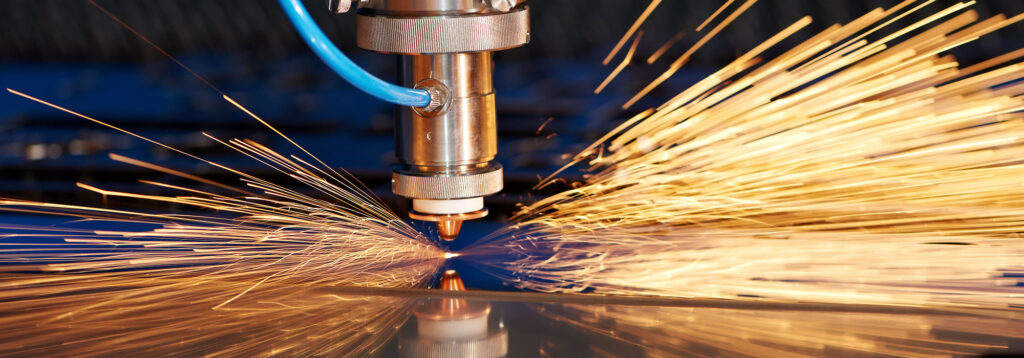
Once the design has been finalized and a working prototype has been produced, the next stage is the fabrication. We can say that this part is where the fun begins. Most people who fell in love with this industry did it after witnessing the process of fabrication. Below we are going to explain how the work is getting done.
Metal fabricators work from design to produce a final product. Each individual piece of the design is cut from metal. This can be done by hand using small machines, or in a large manufacturing environment, it is typically done on a production line using robots and large fabrication machinery – a good example being a car production line.
The car industry is just one of the sectors that have benefited from metal fabrication. It spans across many others, including shipbuilding, construction, aerospace industry, and mining, among many others. It is based on the use of raw, but not only raw materials. It can also find an appliance for castings, fittings, welding wire, plate metal, etc.
People who work in metal fabrication workshops include people from many different avocations, including welders, iron-workers, blacksmiths, and boil-makers, among many others. What is in common for all of them is that they work with metal with the goal of making a final product out of it. These professions provide work for almost 1.5 million people, according to the Bureau of Labor Statistics.
Aluminum extrusion fabrication can eliminate some machining works, making fabrication process more easier and saving more money.
CNC Machining
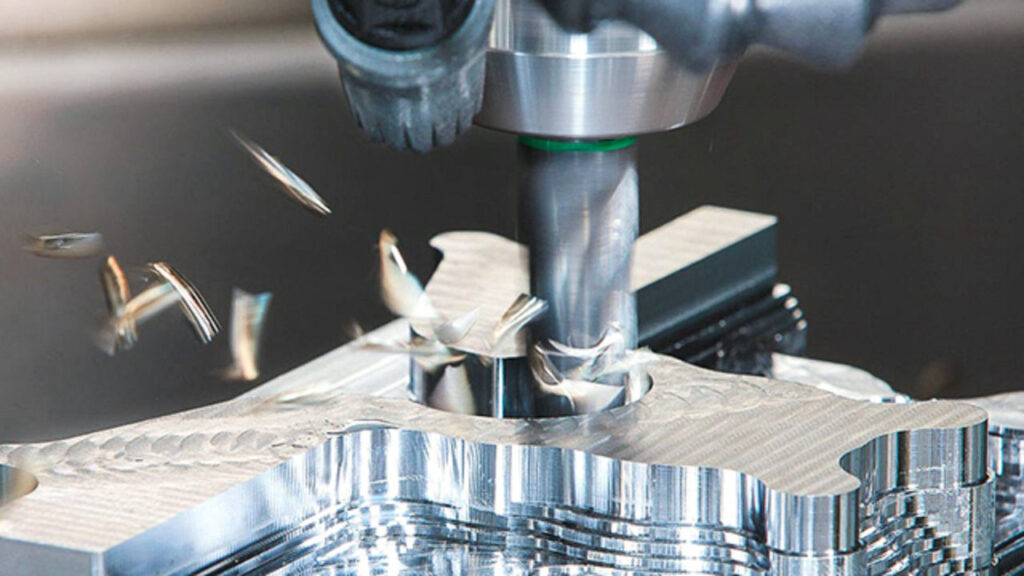
There are many fabrication machines that are purpose-built to carry out specific tasks. For example, a metal fabrication workshop might have a laser cutting machine, roll forming equipment, and a press brake. An experienced machine fabricator will know exactly what machine to use for the task at hand.
CNC machining is used for precision work. These machines use computers to cut metal to an exact specification, usually for highly detailed items such as medical equipment.
The final stage of the fabrication process involves assembling the item and making sure it functions as intended. Some items are then powder coated to ensure they are aesthetically pleasing.
What are the Benefits of Metal Fabrication Shops?
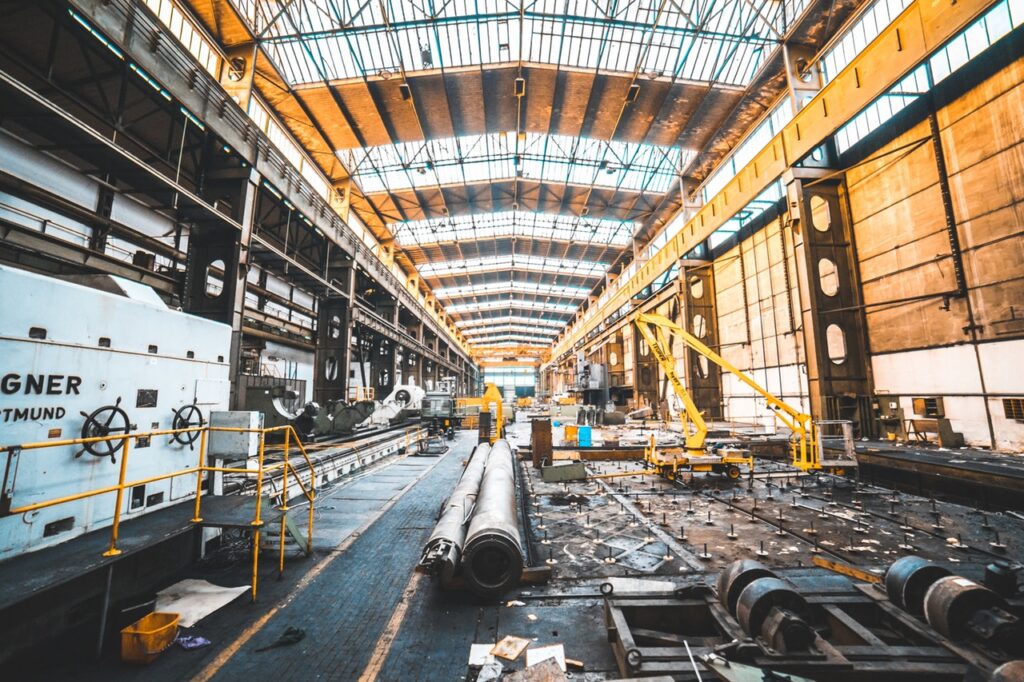
There are many benefits to metal fabrication, but the most important one is centralization. What’s centralized is the number of processes needed for the creation of the final product, with all of them being done in one place. This makes the need for outside vendors and intermediaries redundant. On metal fabrication workshop can replace multiple vendors, which is something the contractors love and why they choose to cooperate with them. It saves both time and money, and it is more efficient than doing a couple of actions separately at different locations.
Other benefits include getting the needed work done by using advanced methods. This scenario is what happens when the work is done by skilled professionals. Companies who are in this type of business are using special machinery. Furthermore, you are going to get precisely what you wanted and what you paid for. This is what separates this branch of the industry from similar ones. With a reputable workshop behind your project, the chances of failure are reduced to zero.
In addition to what we already wrote, you could also pay less for the materials you’ll need. The reason is that workshops with a lot of work already have their suppliers who give them a discount on large purchases. This is not something you could get on your own.
Another essential benefit includes the fact that all the work you have in store is going to be done by skilled workers. We are talking about a specialized branch of the metal industry, and there you won’t find rookies working. In addition to skilled workers, you’ll also get your work done with quality equipment.