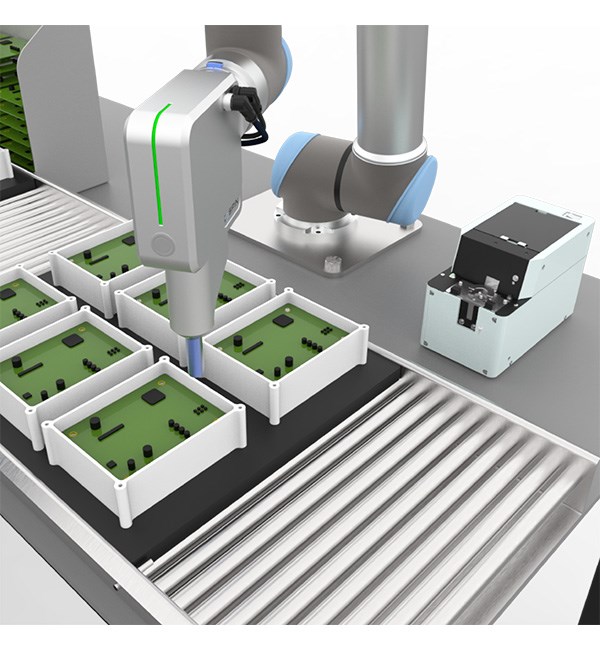
In the rapidly evolving manufacturing landscape, automation and robotics have transformed industrial assembly processes. Driven by the need for precision, efficiency, and flexibility, these technologies are revolutionizing production, allowing industries to meet demands at scales once unimaginable.
Automation and Robotics in Industrial Assembly
Automation and robotics represent a wide array of technologies used in manufacturing to streamline production, reduce human error, and elevate safety standards. Automation includes tools like programmable logic controllers (PLCs) and automated guided vehicles (AGVs) that support workflows, while robotics comprises various robotic systems tailored to specific industrial needs.
In assembly lines, robotics generally falls into several types based on the task complexity and flexibility required:
- Articulated robots ─ Known for their flexibility and range of motion, these robots are widely used for tasks requiring high precision, like welding or part assembly.
- SCARA (Selective Compliance Assembly Robot Arm) robots ─ Ideal for tasks requiring speed and accuracy in a specific plane, often used in electronics and food processing.
- Cartesian robots ─ Known for their linear motion along the XYZ axis, suitable for tasks requiring stability and precision.
- Delta robots ─ Often used in high-speed pick-and-place applications due to their lightweight design and speed.
These technologies empower manufacturers to achieve higher output with consistent quality, enhancing the entire assembly process across industries.
Key Benefits of Automation and Robotics in Assembly Processes
One of the most immediate advantages of automation and robotics is increased productivity. Assembly line robots can perform tasks faster than human workers, maintaining efficiency 24/7 without breaks. This continuous operation reduces cycle times, eliminates bottlenecks, and enables manufacturers to meet production goals more effectively.
Automation tools also facilitate smoother workflows by reducing time-consuming, manual processes. In cases where precision is critical, robotic systems offer faster assembly without compromising accuracy, allowing businesses to expand production without requiring additional labor resources.
Enhanced Precision and Quality
Robotic systems are designed to maintain consistency and precision, which helps reduce waste and enhance product quality. In industries like electronics, where a minor misalignment can result in a defective product, automation’s accuracy is invaluable. Robots can repeatedly perform complex tasks with a high degree of precision, minimizing human error and ensuring uniformity in every batch.
By using vision systems and sensor technologies, robots can also detect minute variations, which would be challenging for human workers. This contributes to higher quality control, enabling manufacturers to confidently meet product specifications and regulatory standards.
Increased Flexibility and Scalability
One of the significant advantages of automation is its adaptability. Robots can be reprogrammed to switch between different tasks, allowing manufacturers to meet varying production demands and adapt to new product lines without significant delays. This flexibility is especially valuable in industries that produce a wide variety of products and need to adapt their assembly lines frequently.
Scalability is another factor: as demand fluctuates, automation can allow manufacturers to scale operations up or down seamlessly. For example, when introducing a new product, companies can implement gradual automation steps to optimize the assembly process while minimizing operational disruption.
Safety and Ergonomics Improvements
Industrial automation and robotics significantly enhance workplace safety. Repetitive tasks, heavy lifting, and high-risk activities traditionally pose dangers for human workers. By assigning such tasks to assembly line robots, manufacturers reduce the risk of injuries, leading to safer working environments.
Furthermore, robots can operate in hazardous environments where high temperatures, toxic substances, or confined spaces are involved. This protection helps prevent accidents and supports overall employee well-being by reducing strain on workers.
Challenges and Considerations in Implementing Robotics and Automation
Implementing robotics and automation often requires significant upfront investment. Costs include purchasing robotic units, software licenses, integration services, and training. However, this investment can yield substantial long-term benefits in terms of productivity gains and reduced labor costs.
Conducting a cost-benefit analysis to determine the expected return on investment (ROI) can help justify these expenditures. Additionally, many regions offer incentives or subsidies to promote automation in manufacturing, which can help offset initial costs.
Technical and Workforce Challenges
Automation and robotics require specialized technical skills to operate, maintain, and troubleshoot systems. This can be a challenge for companies with limited technical staff or workforce adaptability. Establishing training programs and reskilling existing staff can bridge this gap, preparing workers to oversee and manage automated processes effectively.
Another approach is to work with automation providers that offer training packages and ongoing support, ensuring that employees are prepared to handle new technology.
Integration with Existing Systems and Processes
Integrating automation into existing manufacturing systems can be complex, especially for facilities with legacy infrastructure. Compatibility issues can arise, requiring careful planning and potentially custom solutions to ensure smooth interoperability.
A phased approach to automation can help companies transition without disrupting daily operations. Gradually introducing robotics in one area of the assembly line, for example, allows for a smoother transition and provides insights for future implementations.
Conclusion
Automation and robotics are transforming industrial assembly, providing manufacturers with the tools to boost productivity, enhance quality, and promote safety. While initial investments and technical challenges exist, the long-term benefits—ranging from increased flexibility to scalable production—are substantial.
For industries looking to remain competitive in an era defined by rapid technological advancement, exploring assembly line robots and automation solutions is not just an option; it’s a strategic necessity.