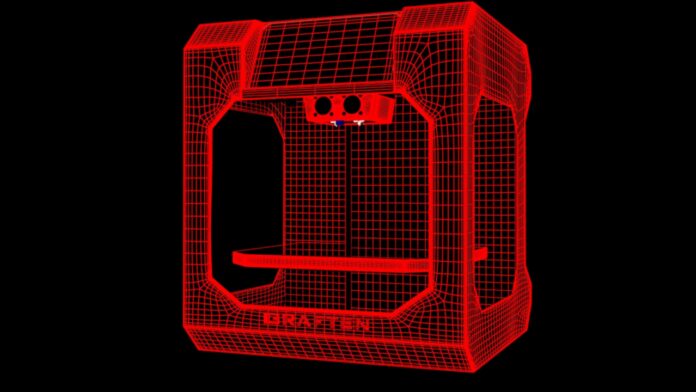
3D printers have revolutionized the manufacturing industry, rapidly transforming the way goods are produced and distributed. This amazing technology has become increasingly accessible to businesses of all sizes and ages, thanks to its affordability and availability of materials. But one question remains: What file formats do 3D printers use?If you’re a beginner or someone just starting out with 3D printing, you might be wondering the same thing.
Understandably, getting familiarized with the different formats used by 3D printers can seem intimidating at first. From STL files to G-codes and beyond, it can be tough to understand which type of file you need to work with.In this blog post, we’ll provide an in-depth guide to the different 3D printing file formats and explain when and why each type is used. So if this is something that’s been on your mind lately – read on!
The file format is essential to a successful 3D printing experience. It’s what keeps the printer in sync with the digital file containing instructions and helps manage the transportation of information. In order to understand how a 3D printer functions, it’s important to understand a little bit about the types of files they are able motion and operate on.
The debate in this area these days is whether open source or proprietary file types are better for 3D printing. Open source file types have been around since the early days of 3D printing. Being open source allows others to freely use and modify the software, thereby creating improvements over time that can be applied to the entire community.
However, some argue that keeping the technology proprietary yields greater levels of security and control vs allowing the data to be shared among multiple stakeholders.
Read about the best color printer for a small business.At the end of the day, much of which file type you opt for depends on which best meets your particular needs and offers advantages like cost savings, improved security, sharing flexibility etc. Whatever decision you make just be sure to do your homework first as every technology has strengths and weaknesses depending on user objectives.Now that we’ve covered an overview of understanding what file formats are used by 3D printers lets move into deeper look into the various types of formats available to choose from.
Types of File Formats Used by Printers
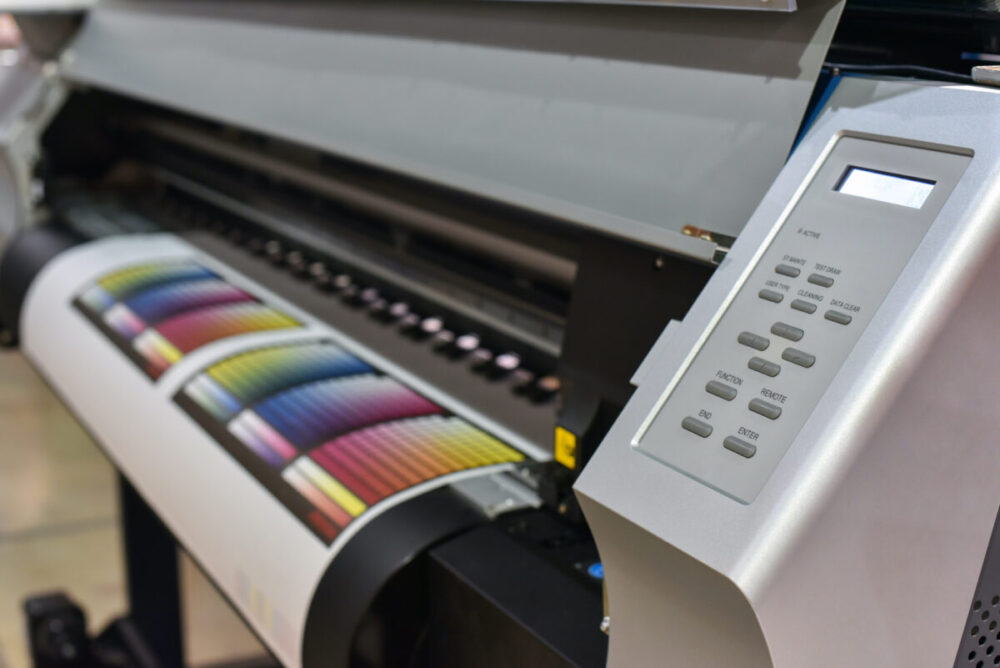
Now that we have a better understanding of what file formats are, let’s dive into the different types that are typically used by 3D printers. The most common, and arguably the most useful, is the STL format. Splitting its name into “STereoLithography” this type of file is often referred to as a “triangle mesh” because it divides 3D models into triangles which gives printers an easier time replicating and building.
Additionally, STL files can be opened in a wide variety of software including Meshmixer and Maya3D, to help manipulate and shape the model before printing.Another type of file format used by 3D printers is OBJ. Short for “Object” this format has been able to gain traction due to its ability to represent both color and texture along with the geometry of the model being printed. While OBJ files tend not to have great support when it comes to 3D printing software, they offer a strong range of applications given their level of detail and compatibility with design tools such as Cinema 4D and Blender3D.
One other lesser-known file format used by many 3D printers is VRML, which stands for Virtual Reality Modeling Language. Unlike STL and OBJ which are considered mesh formats, VRML can contain both mesh data as well as curves representing an entire surface with mathematical precision. This makes it accurately represent complex geometric specifications for printing, however due to its more specific nature it does not have much versatility with design programs outside of specialized software like Anim8or and Daz Studio 4 Pro.File formats provide an essential framework for any 3D printer whether it be for creation or replication purposes.
We may debate on the best way to approach different scenarios but ultimately the choice of format should be based on what best suits the project being printed while also taking into account aspects like cost-efficiency and production time. As we continue to explore further into the world of 3D printing, having an understanding of these types will help inform our decisions as to which output results in a satisfactory end product.
In order to assess this further, however, we will need to take a deeper look at one particular file type commonly used by 3D printers – STL files.
- The most common 3D printer file format is stereolithography (.STL) as this format can accommodate a wide range of shapes and geometry.
- Other supported file formats for 3D printing include OBJ, GCode, and VRML.
- According to analysis conducted by 3DPrinting.com, 45% of 3D printing enthusiasts prefer to use the STL file format when creating or downloading models for their 3D printers.
STL File Format Explained
STL (stereolithography) is an incredibly important file format for 3D printing. This format, in particular, is used by virtually all 3D printers; it was initially developed by the company 3D Systems in 1987 and became the first widely-used 3D model format.
STL files are generally created via CAD programs and are comprised of triangles that form a mesh to adequately describe the surface geometry of the object that is being printed. This mesh consists of various vertices, or points in space, with their corresponding X, Y, and Z coordinates to define the shape.
When it comes to STL files, many people debate whether higher-quality Meshlab tools are needed versus using less reliable versions with fewer facets. The argument of higher-quality versus lower-quality can largely be seen as a tradeoff between generation time and quality: many argue that though more facets create a more accurate shape, more facets also require more processing time and usually mean a longer wait before printing can begin – which can cause tedious delays.
Nevertheless, higher-fidelity meshes generally produce smoother shapes that also minimize potential defects when printing objects with complex curves or other intricate details.Overall, STL remains one of most commonly used file formats due to its reliable accuracy and compatibility across multiple platforms. The versatility of STL files allows for many different types of 3D printing applications from medical models to items like toys or sculptures – making them an essential part of the 3D printing process.
In order to fully benefit from this type of format however, understanding how to generate and prepare STL files beforehand is key for efficiently achieving good results without any major setbacks during the actual printing process.
Moving forward then in order better understand this process as well as further improve one’s chances for success in 3D printing, it’s necessary to look into all aspects of what goes into the build up from small layers during the 3D printing processs.
Layer-By-Layer Process for Printing
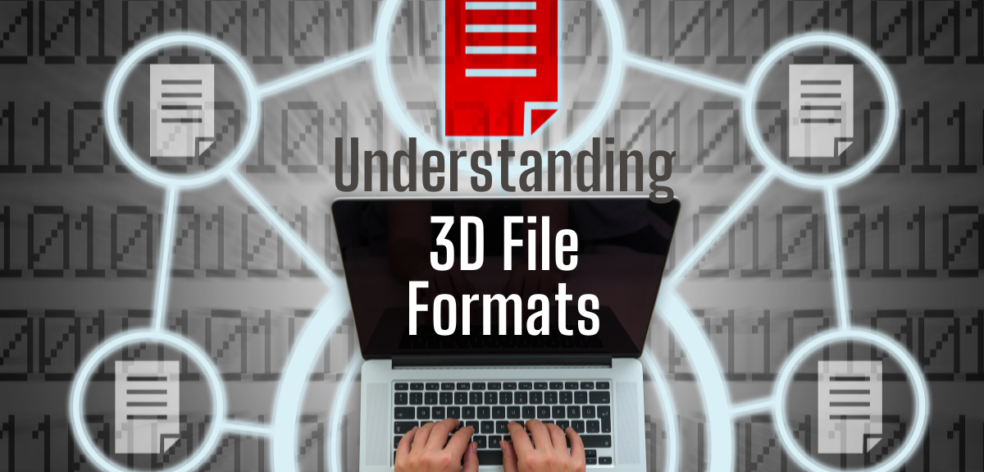
The STL file format is essential to 3D printing, as it tells the 3D printer how to construct objects layer-by-layer. This method of fabrication works by depositing and then bonding an appropriate material layer after layer at pre-defined locations that are derived from a 3D surface model.
The layers stack on top of each other in order to form the final product. Thus, the accurateness and precision of the finished product is largely dependent on the resolution with which it can lay down these layers.The use of a layer-by-layer process for printing results in several advantages, particularly when compared to other manufacturing processes.
More complex and intricate shapes can be made because no machining tools are needed to remove material from the job. This type of fabrication also allows for quick prototyping, so that researchers and engineers can easily modify their design according to feedback they receive during product development.
Furthermore, this process typically results in low waste production, both in terms of materials and time required for setup or resetting computers or machines.Despite the advantages offered by layer-by-layer fabrication, there are some drawbacks associated with this method as well. In some cases, the dimensional accuracy of the final product may not be up to par with more traditional manufacturing methods due to layer thickness and warping over time resulting from heat generated during operation. Additionally, since most 3D printers have a limited bed size, any large components will require separate parts that need to be combined after printing–typically through gluing–which can add additional cost and complexity.
Overall, a layer-by-layer process for printing provides many benefits as well as some potential drawbacks. For those who understand its limitations and work within them, this type of fabrication can prove to be an extremely viable option for creating objects quickly and efficiently.
In order to make sure their designs remain intact throughout their prints however, designers must know how to properly save their models as STL files–the standard file format used by 3D printers worldwide–as discussed in the next section.
Saving Files as STL Files
The STL file format is the most commonly used for 3D printing. An STL (Standard Tessellation Language) file is a representation of a 3D model as a collection of faceted data points.
It is saved in a binary form and one of the most important advantages of it is that virtually all 3D modeling programs can export the models to this file format for the purpose of 3D printing. It enables users to transfer designs from their computer screen into the real world.
The STL files are popular among 3D printer users because they are platform-independent, meaning that regardless of the 3D authoring program used, an STL file can be decomposed and read just fine by any 3D printer. However, STL files do have some drawbacks too.
The translation process from a CAD design to an STL file sometimes causes errors in the input data due to their exact nature and computing algorithms during the transition. As a result, when saving an STL file, it may not always accurately represent the final printed product.
This means that users must manually check their models before 3D printing them, to ensure there aren’t any errors or mishaps in the output.Overall though, with proper checking and supervision on behalf of the user, STL files are ideal for bringing physical objects from digital designs into reality.
With effective manipulation of these files, users will be able take full advantage of 3D printing technology and benefit from its wonders. After all that’s taken care off, it’s time to look at another layer in 3D printing: which softwares can be used in order to manipulate and edit files in preparation for printing.
Programs Used to Manipulate and Edit Files
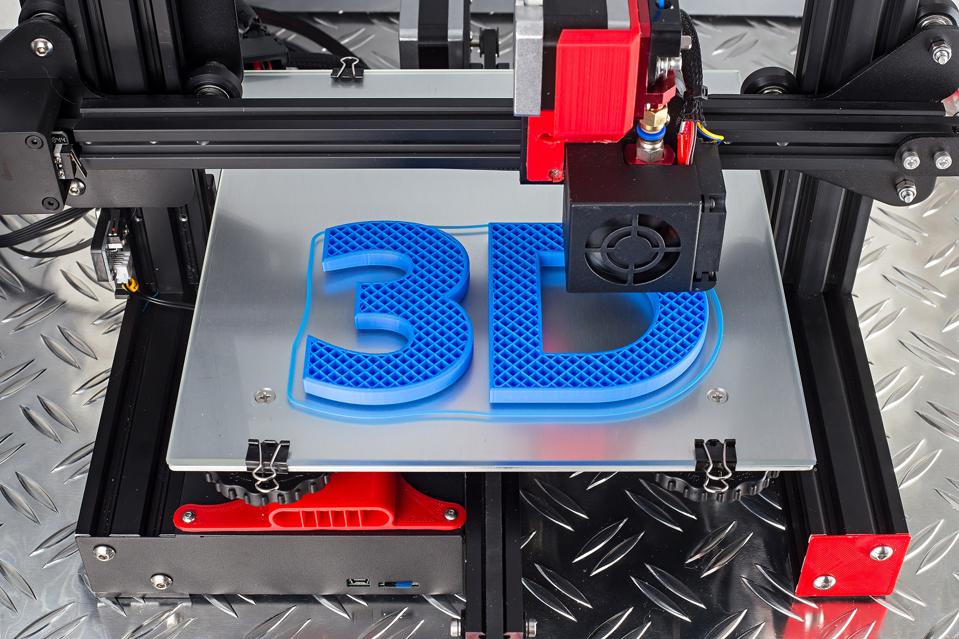
Now that you know how to save your 3D models as STL files, let’s take a look at what programs are used to manipulate and edit them. These software programs vary widely, depending on the type of project you’re working on.
However, common software applications used for 3D printing projects include CAD (Computer-Aided Design), CAM (Computer-Aided Manufacturing), and CAE (Computer-Aided Engineering). Each of these types of software is designed to provide a certain set of features that help improve the accuracy and efficiency of 3D printing.CAD Packages are designed to provide extensive modeling capabilities, allowing users to alter nearly every aspect of the model they’re working with.
They enable users to move, rotate, and scale objects, adjust lighting effects and camera positions, manage textures and materials, and more. CAM Packages are focused on generating the toolpaths that control mechanical tools during the fabrication process. This allows users to define the exact paths a printer will take when creating various models or designs.
Lastly, CAE Packages are focused on simulating and analyzing different types of physical systems in order to identify any weaknesses prior to manufacturing. By leveraging the power of advanced physics engines, equations, numerical techniques, and analytics capabilities, these packages can help 3D printers produce consistent results in less time.
The type of model manipulation program you choose will depend largely on your specific needs. If you plan to work with complex models that contain multiple parts or intricate pieces then it’s likely that a CAD package would be most beneficial. On the other hand, if you need to quickly generate toolpaths then CAM packages would be better suited for this purpose.
Regardless of which type of software application you use, their ultimate goal remains the same: empowering 3D printers with an efficient process for accurately producing desired results.Due to the wide range of features that each type of program offers, it can often be difficult to determine which one is right for your project. Seeking out feedback from peers or professionals who have experience in this field is always a good starting point if you find yourself unsure about which option is best.
With this extra insight into different applications and their respective advantages, you may find it easier to make an informed choice about which one ultimately fits your needs perfectly.Aside from manipulation programs specifically made for 3D printing purposes, standard editing software such as Photoshop can also be useful for customizing images before they are sent off for production.
While many people prefer not to use image editing tools for their personal projects due to reasons related to personal taste or design technique preference, having access to this type of application provides additional convenience when it comes time to fine-tune certain details before printing begins.With so many potential file formats available as well as several software options available for manipulation and editing purposes, it’s no wonder why 3D printing has become such a popular hobby over the past few years.
To learn even more about how these processes work together throughout the life cycle of a 3D printed item we must now turn our attention towards understanding some additional features that make up the STL file format itself.
Additional Features of the STL File Format
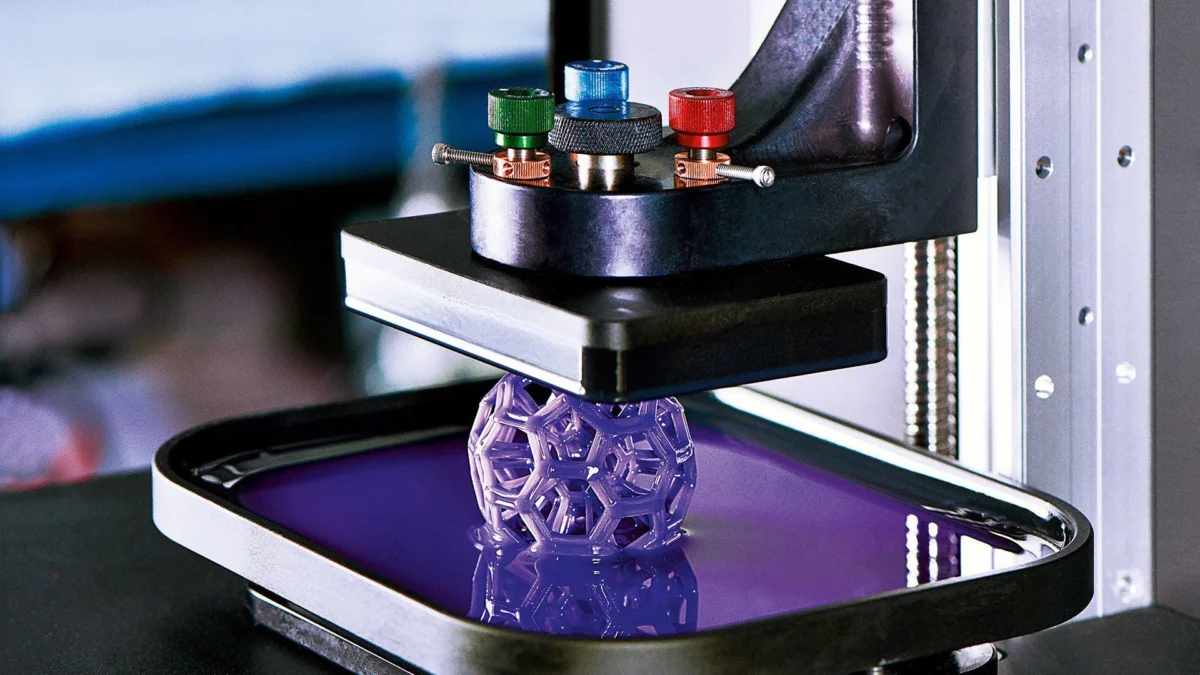
The STL file format is often regarded as the de facto choice for 3D printing because of its accessibility and versatilty. This format has several additional functions that make it a useful tool when creating 3D models.
STL files have a built-in feature known as tessellation, which allows for an increased level of detail in the geometry of the models. The algorithm used by the STL system divides each surface into smaller triangles or facets, thus increasing the complexity of the model without causing any difficulty to render or print. By using these triangle faces, users can create curved surfaces that look smooth in their final renditions despite being composed of only a few complex poly-gons.
This makes STL an ideal choice for both designers and 3D printers alike, as it offers a degree of flexibility and detail not found in other formats.When it comes to describing how an object looks, the STL file format also has something that others do not – a surface normal quality. Face normals are directional vectors that describe where each face points outward and provide information about orientation and direction.
These vectors help create even more realistic looking prints and make it easier to determine whether two objects are colliding, making them an invaluable tool for animators and video game engineers working with physical simulations.While there are some advantages to using an STL file format, there are also some drawbacks associated with it. Despite being adequately detailed for many uses, these files cannot represent details better than 0.001mm due to their limited tesselation capability, which means large amounts of small details will not be correctly represented in printed objects.
Additionally, STL files lack a method for properly conveying color information to 3D printers, leaving color reproductions either seemingly impossible or prone to errors from using RGB values instead of Pantone colors that match closely enough with the original design.In conclusion, while there are some limitations to using this file format for 3D printing, the additional features found within STLs still make it stand out compared to other options available in terms of print resolution and accuracy.
With proper experience under its belt, anyone can use this versatile system for various types of project and achieve astonishing results with very little effort
Frequently Asked Questions and Their Answers
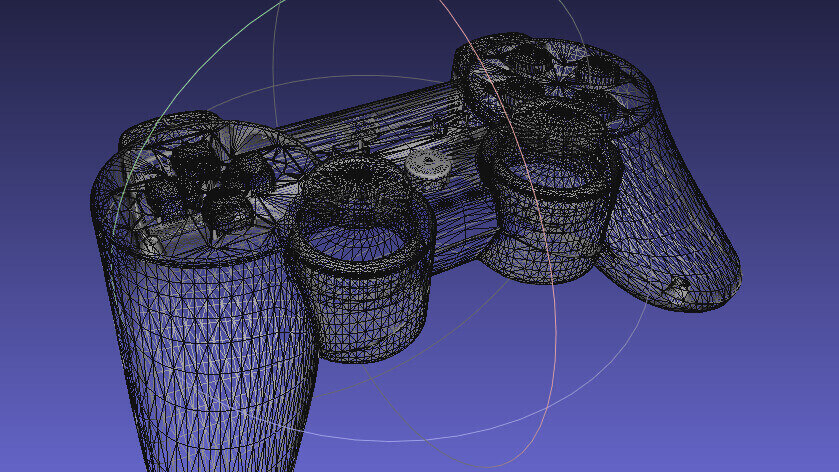
Can 3D printer files be printed from any type of computer?
Yes, 3D printer files can be printed from any type of computer. Files for 3D printing can come in a variety of formats, but the most popular are STL and OBJ.
These files are simple to read and send to a 3D printer, regardless of the operating system or hardware used. Furthermore, special 3D printing software helps to further simplify the process by being designed to work on many different types of computers, with support for CAM (Computer Aided Manufacturing) commonly built-in.
For example, popular options such as Autodesk’s Meshmixer and TinkerCAD are compatible with various operating systems and hardware platforms.
What software is typically used to generate 3D printer files?
The software used to generate 3D printer files varies depending on what type of 3D printer you are using. Generally speaking, the most commonly used programs for 3D printing are CAD (Computer Aided Design) programs like SolidWorks, Autodesk Inventor, and Fusion 360; these programs allow users to create complex designs for 3D printing. Additionally, specialized programs like Cura and Simplify3D are designed specifically for 3D printers and include slicing capabilities that allow users to slice their designs into slices that the 3D printer can understand and put together.
What is the most common type of 3D printer file format?
The most common type of 3D printer file format is STL (Stereolithography), which stands for Standard Tessellation Language. This format, developed by 3D Systems in 1987, is the de facto industry standard for 3D printing, used for creating digital three-dimensional models from CAD (Computer Aided Design) software.
It is supported by all major 3D printing software and hardware, allowing it to be easily exchanged and adapted across platforms. STL has an advantage over other commonly used 3D printing formats due to its tessellation algorithm, which creates a tightly compressed mesh made up of triangles that are optimally placed during the conversion process to make the most effective use of material in the build. This means parts can be printed quickly, with minimal waste and improved accuracy.