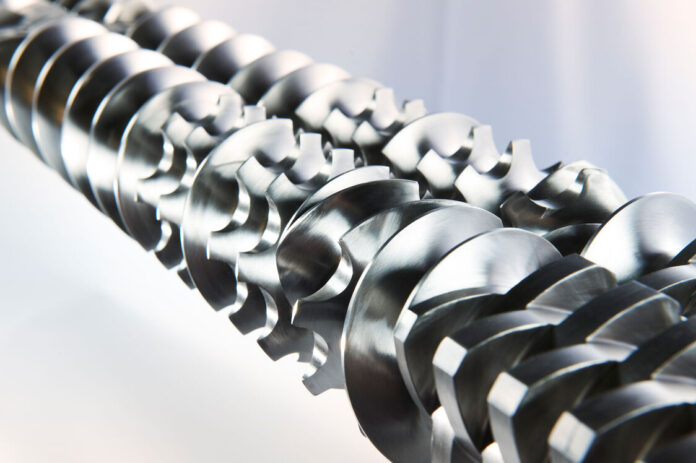
In the field of material processing and manufacturing, twin screw extruder technology has undergone a remarkable evolution, driving innovation and revolutionizing various industries. From its humble beginnings to its current state-of-the-art capabilities, the journey of twin screw extruders is a testament to the relentless pursuit of efficiency, versatility, and precision in modern engineering.
Origins and Early Development
Twin screw extruders have been around for over a century, with their origins dating back to the late 19th century. Initially developed for the rubber industry, these machines were primarily used for mixing and compounding rubber compounds.
However, it wasn’t until the mid-20th century that the twin screw extruder technology began to gain traction in other industries, such as plastics, food processing, and pharmaceuticals.
Advancements in Design and Functionality
Over the years, twin screw extruder technology has undergone significant advancements in design and functionality. Early models were typically co-rotating, with two screws rotating in the same direction.
However, as demand for higher throughput and enhanced mixing capabilities grew, counter-rotating twin screw extruders were developed, featuring screws rotating in opposite directions.
Enhanced Mixing and Dispersion
One of the key advantages of twin screw extruders is their ability to achieve superior mixing and dispersion of materials. This is made possible by the intermeshing or non-intermeshing design of the screws, which creates multiple zones of intense shear and elongational flow.
As a result, twin screw extruders can produce homogeneous blends, dispersing additives uniformly, and achieving precise control over material properties.
Versatility in Material Processing
Another notable aspect of twin screw extruder technology is its versatility in material processing. These machines can handle various materials, including thermoplastics, thermosets, elastomers, and food products.
With the ability to control parameters such as screw configuration, barrel temperature, and residence time, twin screw extruders offer unmatched flexibility, allowing manufacturers to tailor processes to meet specific requirements.
Integration of Advanced Control Systems
In recent years, the integration of advanced control systems has further enhanced the capabilities of twin screw extruders. From PLCs (Programmable Logic Controllers) to HMI (Human-Machine Interface) systems, these technologies enable precise monitoring and control of process parameters, ensuring consistency and quality in every batch.
Data acquisition and analysis advancements have also facilitated real-time optimization and troubleshooting, maximizing efficiency and productivity.
Applications Across Industries
The versatility and efficiency of twin screw extruders have made them indispensable tools in a wide range of industries. From compounding and masterbatch production in the plastics industry to food processing and pharmaceuticals, these machines play a vital role in manufacturing processes worldwide.
Whether producing polymer blends with improved properties or extruding high-quality food products with precise texture and flavor, twin-screw extruder technology continues to push the boundaries of what is possible.
Looking Ahead: Future Innovations
As technology continues to advance, the future of twin screw extruder technology looks promising. From advancements in materials and screw designs to the integration of artificial intelligence and machine learning, the possibilities for innovation are virtually limitless.
With ongoing research and development efforts aimed at improving efficiency, sustainability, and performance, twin screw extruders are poised to remain at the forefront of material processing and manufacturing for years to come.