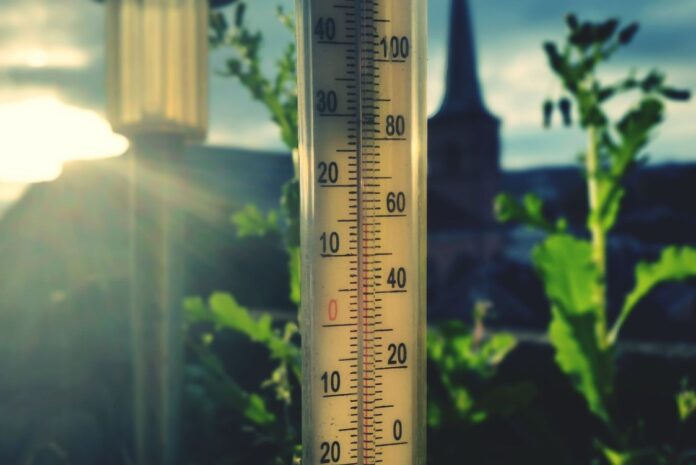
The world of product testing is vast and intricate, encompassing various methods, instruments, and technologies. One of the indispensable tools that stand out in this realm is temperature cycling test chambers.
These chambers play a pivotal role in ascertaining the durability and reliability of products under fluctuating temperature conditions.
By simulating varying temperature environments, these chambers offer a controlled setting to evaluate a product’s performance, material stability, and overall lifespan.
Let’s delve deeper into the significance and utility of these test chambers in the realm of product testing.
Functionality and Design of Cycling Test Chambers
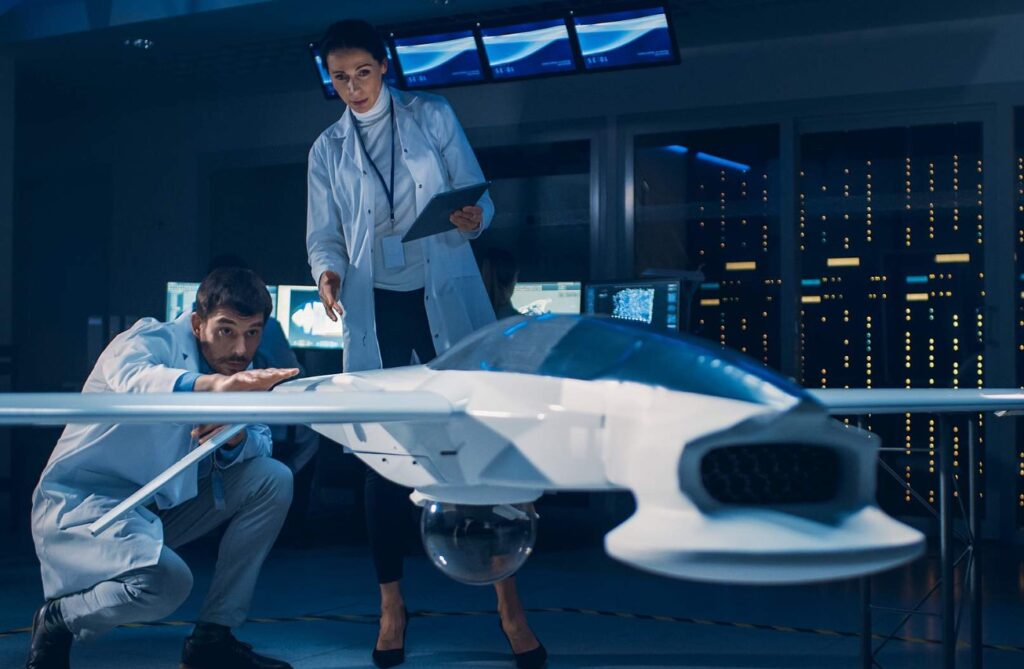
The primary function of the temperature cycling test chambers is to replicate the temperature fluctuations that a product might face during its lifecycle.
These chambers are ingeniously designed to mimic a wide range, from the cold of Arctic winters to the blistering heat of desert summers.
Built with insulated walls, the internal environment of the chamber is controlled by heating and cooling systems, sensors, and controllers that ensure precise temperature adjustments.
Products or materials placed inside the chamber undergo rapid temperature transitions, allowing testers to observe their reactions and evaluate their resilience.
Applications Across Industries
The value of temperature cycling test chambers transcends industries. For instance:
- Electronics and Semiconductors: Here, temperature cycling helps ascertain the longevity and robustness of electronic components. By repeatedly exposing them to fluctuating temperatures, potential weak points, such as solder joints or connections, are identified.
- Automotive: In this sector, components such as engine parts, lighting systems, and internal electronics are tested to ensure they can withstand the variations experienced in real-world driving conditions.
- Aerospace and Aviation: With the extremes of temperature experienced during flights, especially during take-offs and landings, it’s crucial to test components like sensors, communication devices, and other onboard systems in cycling chambers.
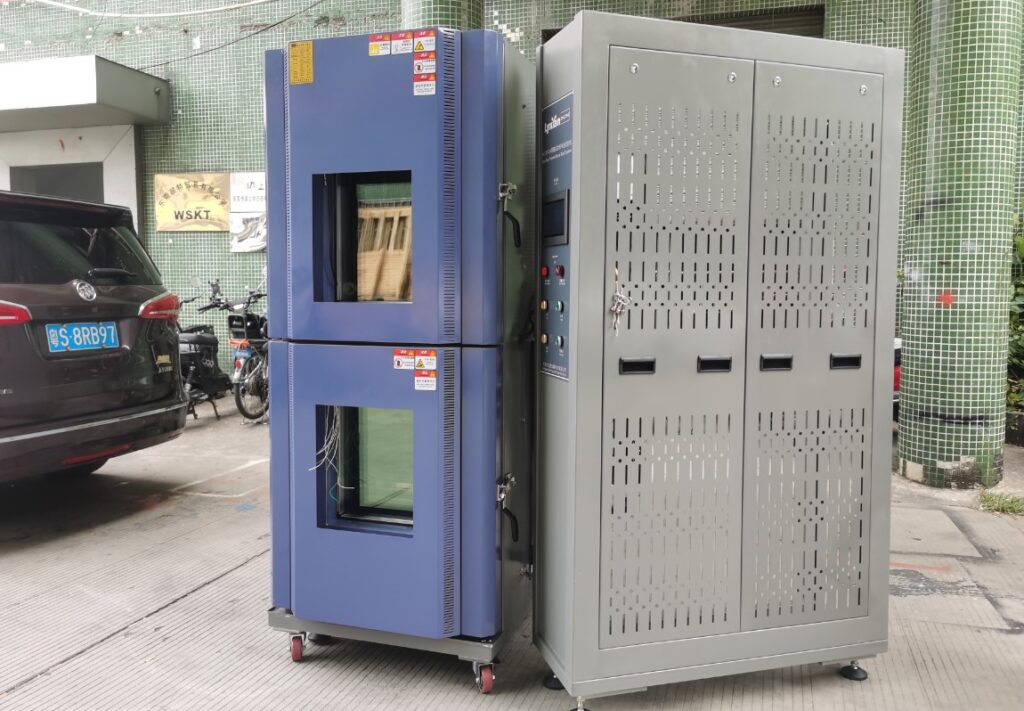
Advantages of Cycling
- Reliability and Quality Assurance: One of the most significant benefits of using these test chambers is the assurance of product reliability. When products undergo rigorous testing and emerge unscathed, manufacturers can confidently claim their quality and durability.
- Cost Savings: By identifying potential product flaws early in the design or production process, companies can avoid costly recalls or redesigns later. Thus, investing in thorough temperature cycling tests can result in substantial long-term savings.
- Enhanced Reputation: Companies that regularly subject their products to stringent tests and uphold high-quality standards often enjoy a better reputation in the market. Customers tend to trust and remain loyal to brands that prioritize quality and reliability.
- Eco-friendly Disposal: Products that last longer reduce the need for frequent replacements. This longevity translates to less waste in landfills and a reduced carbon footprint, contributing positively to environmental conservation.
Conclusion
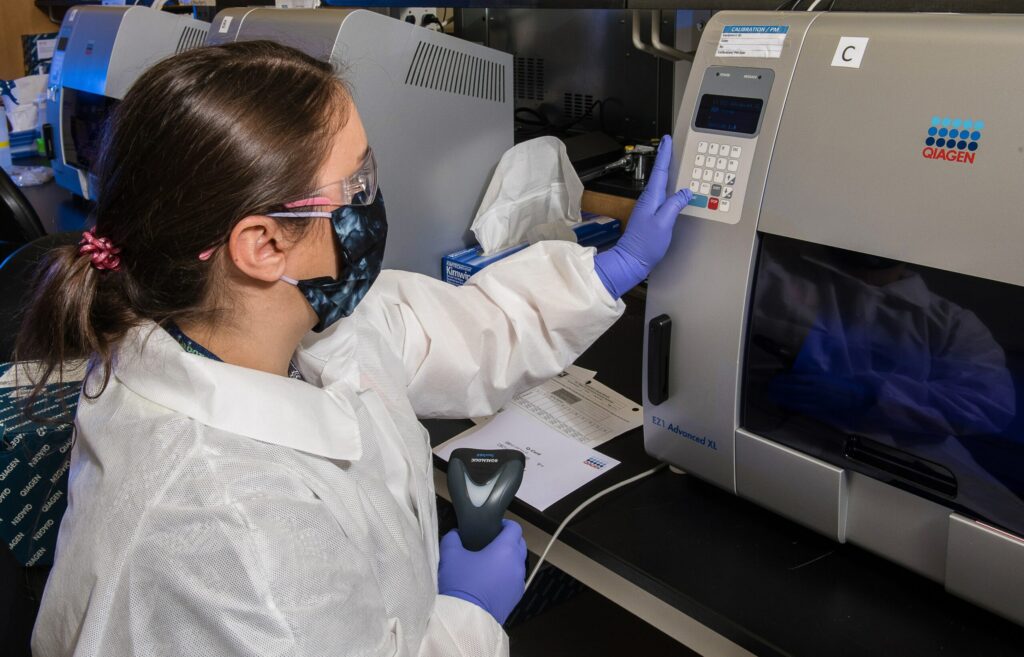
Temperature cycling test chambers stand as beacons of innovation and quality assurance in product testing.
They not only guarantee that products can withstand the rigors of fluctuating temperature environments but also ensure that they do so over an extended period.
By simulating extreme variations, these chambers provide invaluable data that helps industries refine their products, ensuring they are both durable and reliable.
In a world where product quality and durability are paramount, these test chambers will undoubtedly continue to play a vital role in shaping the future of product development and testing.